How to Prevent Hot Cracks in Casting Parts?
- Share
- Issue Time
- Apr 9,2021
Summary
We all know that the application of castings is very wide. At present, it has been used in hardware and the whole mechanical and electronic industry. So how should we prevent the generation of hot cracks?
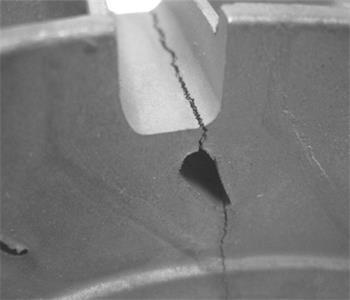
Most people do not understand the cause of the hot crack in casting parts, including the die casting, which may produce a hot crack, then we need to identify a cause of the hot crack and prevent its generation.
Definition of hot crack
Cracking is the shape of crack, winding fracture are try very irregular, and the surface is wide, the in the narrow, belong to hot crack with the mechanism that began after condensation, molten steel into mold cavity when the crystal structure has been formed and began to line contraction, at this time due to the internal steel has not completed the solidified into a solid shrink is blocked, can cause stress in the casting or plastic deformation, when they are more than the material of under the high-temperature ultimate strength, the casting crack.
The cause of thermal crack formation
After the liquid metal is poured into the mold, the heat loss is mainly through the mold wall, so solidification always begins at the surface of the casting. Solid shrinkage occurs when a large number of dendrites are overlapped to form a complete skeleton at the later stage of solidification. However, there is still a layer of the unsolidified liquid metal film (liquid film) between the dendrites. If the shrinkage of the casting is not hindered by any hindrance, then the dendrite skeleton can shrink freely without being subjected to force. When the shrinkage of the dendritic skeleton is hindered by sand mold or sand core, tensile stress will occur if the dendritic skeleton cannot shrink freely. Cracking occurs between dendrites when the tensile stress exceeds the ultimate strength of the material. If the dendritic skeleton is pulled apart slowly and enough liquid metal around the pulled part flows into the crack site in time to replenish, no thermal cracks will occur in the casting. On the contrary, if the crack is not replenished by liquid metal, hot cracks will occur in the casting.
The causes of hot crack are reflected in the process and casting structure, including casting wall thickness is not uniform too small internal Angle; Lapping part of the fork too much, casting frame, rib block the normal shrinkage of the casting; The sprayer system hinders the normal shrinkage of the casting. For example, the sprayer is close to the box belt or the sand strength between the sprayer is very high, which limits the free shrinkage of the casting. The riser is too small or too large; the Alloy line shrinkage rate is too large; The forming elements of the low melting point phase in the alloy exceed the standard, and the content of sulfur and phosphorus in cast iron is high. Casting box premature sand fall, cooling too fast.
How to prevent thermal cracking
1. Improve cast parts structure
The wall thickness should be uniform, and the corner should be rounded to reduce the stress concentration. The spokes of wheel castings can be bent if necessary.
2. Improve the melting quality of alloy materials
Refining and degassing processes were used to remove oxidizing inclusions and gases in liquid metals. The content of harmful impurities should be controlled, and a reasonable melting process should be adopted to prevent cold cracks.
3. Adopt correct casting process measures
Simultaneous solidification of castings in the casting process of parts is beneficial to prevent not only hot cracks but also cold cracks. Reasonably set the position and size of the pouring riser to make the cooling rate of each part of the casting as uniform as possible and reduce the tendency to crack.
Correctly determine the residence time of the casting in the sand mold. The sand mold is a good thermal insulation container, which can further homogenize the temperature of the thicker and thinner parts of the casting, reduce the temperature difference between them, reduce the thermal stress, and reduce the tendency of cold crack. Extend the stay time of the casting in the mold, so as not to open the box too early in the casting resulting in greater internal stress, and cold cracks.
The effective measures to prevent the cold cracking of the castings due to shrinkage stress are to remove the pressure box iron and loosen the fastening device of the sandbox as soon as possible after the solidification of the castings by increasing the recalcitrance of sand mold and sand core. The sand mold and core of large castings can be excavated in advance after pouring to reduce their shrinkage resistance to the casting and promote the uniform cooling of each part of the casting. In the process of falling sand, cleaning and handling of castings, collision, and extrusion should be avoided to prevent cold cracks in castings.
4.aging heat treatment
For castings with high casting stress, aging treatment should be carried out in time to avoid cold cracks caused by excessive residual stress. If necessary, aging heat treatment should be carried out after casting riser cutting or welding repair
Our sand castings can be very good to prevent the generation of hot cracks, precision casting process and its own material in the prevention of hot cracks part is done quite well. So if you are interested in casting, please contact us immediately!