3 Process Methods for Machining Parts
- Share
- Issue Time
- Jun 9,2021
Summary
The machining process of mechanical parts will directly affect the entire production process and even the quality of the product. This article will specifically introduce the three processing methods of mechanical parts processing.

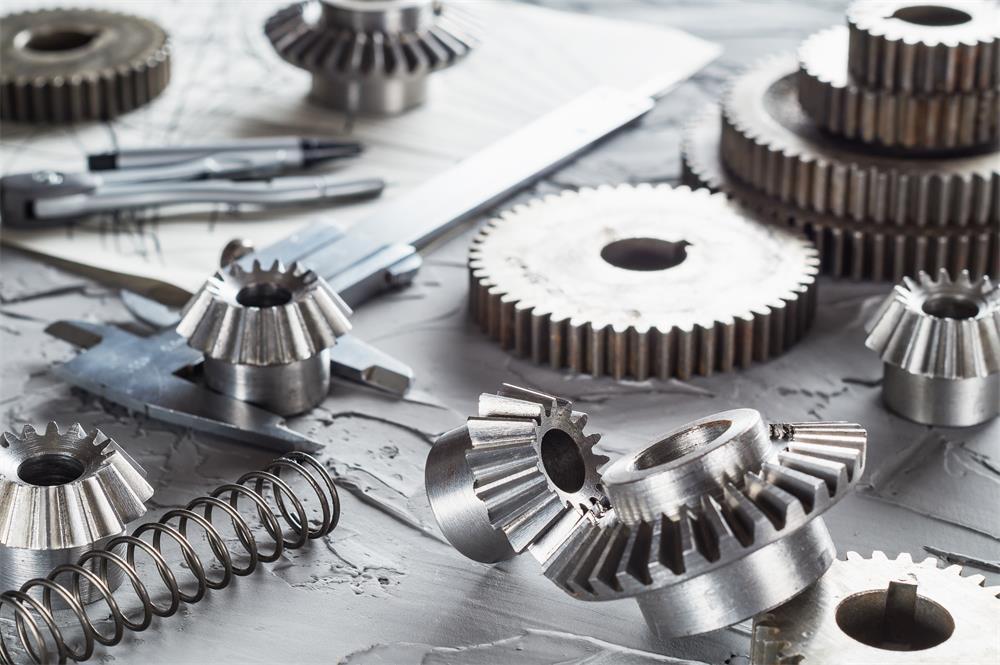
In the process of machining mechanical parts, changing the size, size, position, and shape of the parts according to technical standards and correct parameters is what we often call the machining process of mechanical parts. The machining process of mechanical parts is an important part of the production process, and it will directly affect the entire production process and even the quality of the product. The following are three process methods for machining mechanical parts.
Material removal manufacturing process
The material removal manufacturing process is to remove excess material from the workpiece in a certain way to obtain machine basic parts of the required shape and size. This type of process requires sufficient excess material on the surface of the workpiece. In the process of material removal, the workpiece gradually approaches the shape and size of the ideal part. The greater the difference between the shape and size of the raw materials or blanks, the more materials are removed, the greater the material loss, and the more energy consumed during the processing. Sometimes the volume of lost material even exceeds the volume of the part itself.
Although the material utilization rate of the material removal process is low, it is still the main means to improve the quality of parts, and it also has strong processing adaptability and is the most widely used processing method in manufacturing. The combination of the material removal process and material forming process can greatly reduce the consumption of raw materials. With the development of cutting-edge technology (precision casting, precision forging, etc.), the utilization rate of materials can be further improved. When the production quantity is small, in order to reduce the investment in the material forming process, it is also economical and reasonable to simply adopt the material removal process.
There are many processing forms of material removal technology, including traditional cutting and special processing.
Cutting is a process that uses metal cutting tools to remove excess metal on the workpiece (blank) on the machine tool, so that the shape, size, and surface quality of the workpiece meet the design requirements. During the cutting process, the tool and the workpiece are installed on the machine tool, and the machine tool drives to achieve a certain regular relative movement. During the relative movement of the tool and the workpiece, the excess metal is removed to form the machined surface of the workpiece. Common metal cutting processing methods include turning, milling, planing, broaching, grinding, and so on. There are phenomena such as force, heat, deformation, vibration, and abrasion in the metal cutting process. There is a certain impact on the processing process and processing quality.
Special processing refers to a processing method that uses electrical energy, light energy, etc. to remove material from a workpiece. There are electrical discharge machining, electrochemical machining, laser machining, etc. EDM is to uses the pulse discharge phenomenon generated between the tool electrode and the electrode to ablate the workpiece material to achieve the processing purpose. During processing, there is a certain discharge gap between the workpiece electrode and the tool electrode, instead of direct contact, there is no force in the processing, and conductive materials with any mechanical properties can be processed. In terms of technology, its main advantage is that it can process complex-shaped inner contour surfaces and convert its processing difficulty into outer contour processing, so it has a special role in mold manufacturing. Due to the low metal removal rate of EDM, it is generally not used for the shape processing of the product.
Material forming manufacturing process
The material forming manufacturing process mostly uses models to make raw materials into parts or blanks. The shape, size, organizational state, and even the combined state of the raw materials will change during the process of material becoming scraps. Since the forming accuracy is generally not high, the material forming manufacturing process is often used to manufacture the blank. It can also be used to manufacture parts with complex shapes but not very demanding precision. The production efficiency of the material forming process is high. Commonly used forming processes include casting, forging, powder metallurgy, and so on.
Cast
Casting is a process in which liquid metal is poured into a mold cavity suitable for the shape and size of the part, and the blank or part is obtained after cooling and solidification. The basic technological process is modeling, smelting, pouring, cleaning, and so on. Due to the mold filling ability, shrinkage, and other factors during alloy casting, the castings may have uneven structure, shrinkage, thermal stress, and deformation, which make the precision, surface quality, and mechanical properties of the castings poor. Nevertheless, due to its strong adaptability and low production cost, casting processing is still widely used. The shape is complex, especially the rough part with a complex inner cavity is often used for casting.
At present, the commonly used casting methods in production include ordinary sand casting, investment casting, metal mold casting, and so on.
Forging
Forging and sheet metal stamping are collectively referred to as forging. Forging is the use of forging equipment to apply external force to the heated metal for plastic deformation to form a part blank with a certain shape, size, and structure. The internal structure of the forged blank is dense and uniform. The metal streamline distribution is reasonable, which improves the strength of the parts. Therefore, forging is often used to manufacture blanks for parts that require high comprehensive mechanical properties.
Forging can be divided into free forging, model forging and tire die forging.
Free forging is to place the metal between the upper and lower abutment irons to plastically deform the metal, which is realized by free flow. Generally used to produce forgings with small batch sizes and simple shapes.
Model forging is to place metal in the die cavity of a forging die to deform. The plastic flow of the metal is restricted by the die cavity. The forming efficiency is high, the precision is high, and the metal streamline distribution is more reasonable. However, due to the high cost of mold manufacturing, it is usually used for mass production. The forging force required for forging with free-form models is large and cannot be used for forging large forgings.
Tire mold forging is to forge metal using tire molds on free forging equipment. Tire molds are simple to manufacture, low cost, and convenient to form, but the forming accuracy is not high. They are often used to produce small forgings with low accuracy requirements.
Powder metallurgy
Powder metallurgy is a process in which metal powder or a mixture of metal and non-metal powder is used as a raw material to produce certain metal products or metal materials through mold pressing and sintering processes. It can not only produce special metal materials but also produce metal parts with little and no cutting processing. The utilization rate of powder metallurgy can reach 95%, which can greatly reduce the input of cutting processing and reduce the production cost, so it is increasingly widely used in machinery manufacturing. Due to the high price of powder materials used in powder metallurgy, the powder has poor fluidity during forming, and the shape and size of parts are subject to certain restrictions. There are a certain amount of tiny pores in the powder metallurgy parts, the strength of which is about 20%-30% lower than that of castings or forgings, and the plasticity and toughness are also poor.
The technological process of powder metallurgy production includes powder preparation, compounding, pressing and forming, sintering, shaping, and so on. Among them, the powder preparation and mixing process are usually completed by the manufacturer that provides the powder.
The material cumulative manufacturing process
The material accumulation manufacturing process gradually accumulates and grows parts in a micro-element superposition. In the manufacturing process, the three-dimensional solid model data of the part is processed by the computer to control the accumulation process of the material to form the desired part. The advantage of this type of process is that it can form parts of any complex shape without the need for tools, fixtures, and other production preparation activities.
The produced prototype can be used for design evaluation, bidding, or sample display. Therefore, this process is also called rapid prototyping technology. Rapid prototyping technology is used in the manufacture of product samples, mold manufacturing, and the manufacture of a small number of parts. It has become an effective technology to accelerate the development of new products and realize concurrent engineering so that the products of enterprises can quickly respond to the market and improve the competitiveness of enterprises.
The rapid development of rapid prototyping technology is very fast, and now several methods have entered the application stage, mainly including light curing method, layered manufacturing method, laser selective sintering method, melting accumulation modeling method, of which the light-curing method is the first rapid prototyping to be put into commercial application. technology.
The machining process of mechanical parts must follow machining manufacturing technology, and the production process must be determined according to the actual situation. If you want to know more about mechanical parts after reading the above, you can contact us for more detailed solutions.
As a professional parts manufacturer, we have rich production experience. We attach importance to refined production management, establish a complete quality inspection system, and will provide you with high-quality products. We also provide thoughtful one-stop service and develop effective solutions according to your needs. If you are interested in our mechanical parts, please contact us immediately!