How to Prevent Fatigue Failure of Machine Parts?
- Share
- Issue Time
- Jun 23,2021
Summary
When a machine part fails due to fatigue, it may affect the normal operation of the machine and even cause failure. This article will specifically introduce methods to prevent fatigue failure of machine parts.
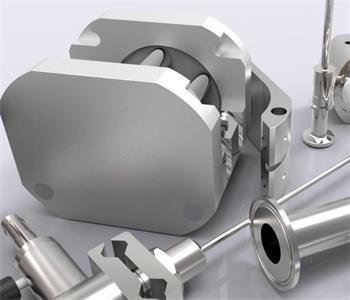
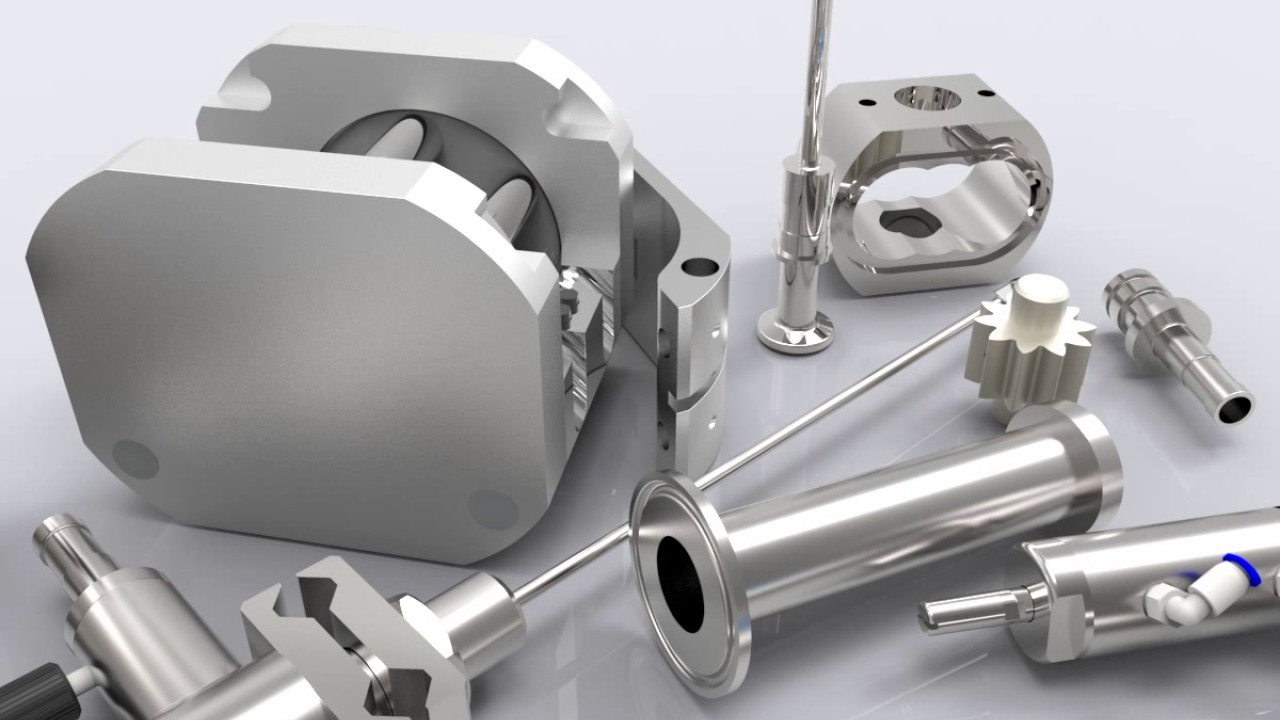
When working with machines or equipment we need to be aware that their parts are subjected to cyclic or variable loads that may lead to a failure due to fatigue. At this time, we need to know the reasons for the fatigue failure of the following machine parts and the preventive measures in the design process.
Fatigue failure may arise due to the following causes
(1)Presence of internal irregularities or discontinuities.
(2)Irregularities resulting from part machining processes themselves.
(3)Part geometry type. This will affect the speed at which cracks will propagate.
(4)Environment influence: thermal fatigue and corrosion fatigue.
(5)The presence of a small crack in a part may also lead to premature fatigue. The ends of the crack are spots where tension builds up, which amplifies the effect of cyclical or variable loads. Cyclical loads cause a state of inner tension that will make the crack grow at its ends since it is at those points where tension concentrates the most. Consequently, the crack will increasingly grow until its sudden failure occurs.
Precaution
1.First, it is necessary to keep in mind that any variation in machine parts are special regions where stress will concentrate, which will affect their machine fatigue strength.
2.A part’s geometry will also affect the speed at which that crack will propagate. A design that favors the emergence of stress concentration areas, cross-section changes, presence of keyways, holes, or inset corners, will enable a crack to develop sooner.
3.The design also has a significant influence on fatigue failure. Any geometric discontinuity acts as a stress concentrator and may become the point of origin of a crack due to fatigue. The sharper the discontinuity, the more severe the stress build-up.
4.Avoiding structural irregularities or revising the design, eliminating sharp changes along the edges that lead to square edges will lead to higher fatigue strength.
5.The dimensions of the part also play a part; increasing their size results in a lower fatigue limit.
6.Improve the surface finish by polishing, to prevent small scratches or grooves that appear on a part’s surface due to cutting.
7.Surface hardening via carburization and nitriding processes where a component is exposed to carbon or nitrogen-rich atmosphere at high temperatures. This layer is usually 1mm deep and harder than the core’s material.
8.Fluctuating or cyclic stress is another aspect to keep in mind. Their loads act for a great number of cycles before failure occurs, being one of the main parameters present in material fatigue strength.
9.An intermediate tensile stress worsens fatigue-related performance in metals since it widens the crack. Conversely, compression stress improves it.
10.Increase performance by means of residual compression stress on a thin surface layer. The overall effect is that the probability of crack nucleation and fatigue failure is reduced.
When designing machine parts, we can increase their fatigue strength, so that they will not easily fail due to high temperature or heavy load, which will affect the operation effect of the machine. If you want to know more information related to machine parts after reviewing the above content, you can contact us for more detailed solutions.
As a professional parts supplier, we have accumulated rich manufacturing experience in this field. We have a professional production team and a complete quality inspection system, which can fully control the quality of products. At the same time, we can also provide corresponding services and formulate effective solutions according to customer needs. If you are interested in our machine parts, please contact us immediately!