Machine Parts Processing-material Removal Manufacturing Process
- Share
- Issue Time
- Sep 29,2021
Summary
The material removal manufacturing process is a commonly used process in machine parts processing, and it’s the main means to provide the quality of the parts. Let's learn about the material removal manufacturing process of mechanical parts.
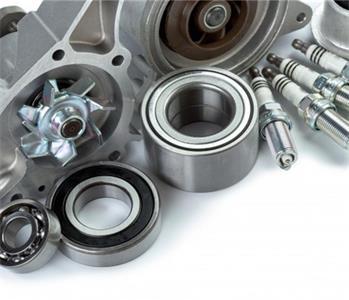
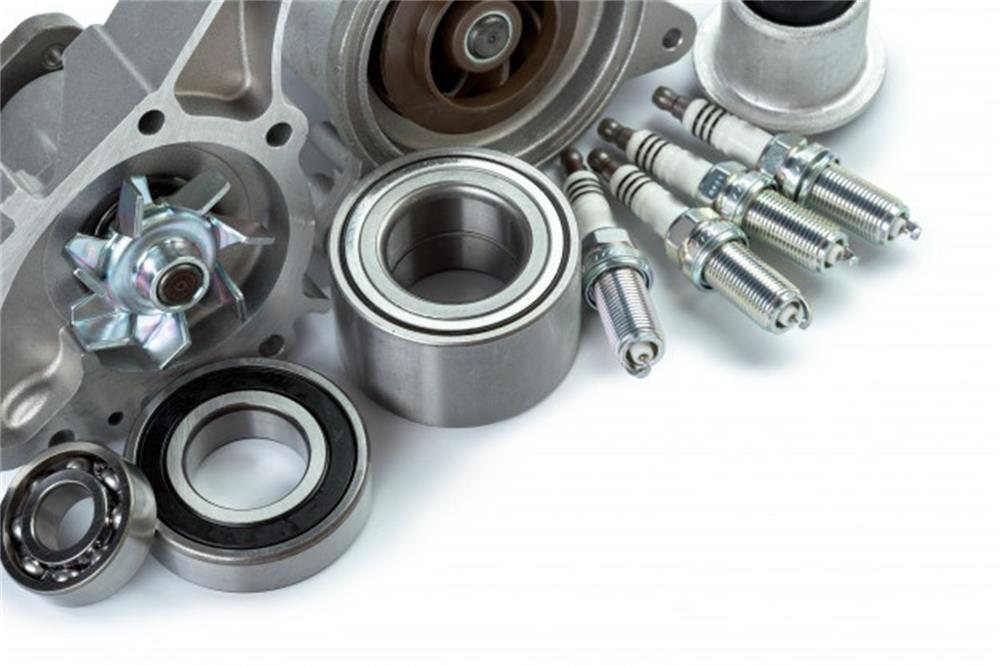
The material removal manufacturing process is to remove excess material from the workpiece in a certain way to obtain machine parts of the required shape and size. This is a very commonly used process in the machining of mechanical parts. The following is the specific information on the material removal manufacturing process.
This type of process requires sufficient excess material on the surface of the workpiece. In the process of material removal, the workpiece gradually approaches the shape and size of the ideal part. The greater the difference between the shape and size of the raw materials or blanks, the more materials are removed, the greater the material loss, and the more energy consumed during the processing. Sometimes the volume of lost material even exceeds the volume of the part itself.
Although the material utilization rate of the material removal process is low, it is still the main means to improve the quality of parts, and it also has strong processing adaptability and is the most widely used processing method in neighboring manufacturing.
The combination of the material removal process and material forming process can greatly reduce the consumption of raw materials. With the development of cutting-edge technology (precision casting, precision forging, etc.), the utilization rate of materials can be further improved.
When the production quantity is small, in order to reduce the investment in the material forming process, it is also economical and reasonable to simply adopt the material removal process.
There are many processing forms of material removal technology, including traditional cutting and special processing.
Cutting
Cutting is a process that uses metal cutting tools to remove excess metal on the workpiece (blank) on the machine tool so that the shape, size, and surface quality of the workpiece meet the design requirements. During the cutting process, the tool and the workpiece are installed on the machine tool, and the machine tool drives to achieve a certain regular relative movement.
During the relative movement of the tool and the workpiece, the excess metal is removed to form the machined surface of the workpiece. Common metal cutting processing methods include turning, milling, planing, broaching, grinding, and so on. There are phenomena such as force, heat, deformation, vibration, and abrasion in the metal cutting process.
Special processing
Special processing refers to a processing method that uses electrical energy, light energy, etc. to remove material from a workpiece. There are electrical discharge machining, electrolytic machining, laser machining, and so on. EDM is to uses the pulse discharge phenomenon generated between the tool electrode and the electrode to ablate the workpiece material to achieve the processing purpose.
During processing, there is a certain discharge gap between the workpiece electrode and the tool electrode, instead of direct contact, there is no force in the processing, and conductive materials with any mechanical properties can be processed.
In terms of technology, its main advantage is that it can process complex-shaped inner contour surfaces, and convert its processing difficulty into outer contour processing, so it has a special role in mold manufacturing. Because of the low metal removal rate of EDM, it is generally not used for product shape processing. Laser processing and ion beam processing are mostly used for micro-processing.
With the advancement of science and technology, in the aerospace and computer fields, some parts that require particularly high machining accuracy and surface roughness require precision machining and superfinishing. If you want to know more about mechanical parts after reviewing the above, you can get a comprehensive solution by contacting us.
As a parts manufacturer, we are always committed to providing customers with quality products and services. We have specialized production equipment and have established a complete quality inspection system to strictly control the quality of our products. At the same time, our complete management team can provide thoughtful one-stop service and formulate effective solutions according to the diverse needs of customers. If you are interested in our machine parts, please contact us immediately!