How to Process the Surface of Machine Parts?
- Share
- Issue Time
- Oct 27,2021
Summary
By processing the surface of machine parts, it can meet the predetermined performance requirements. Let's talk about how to process the surface of machine parts.
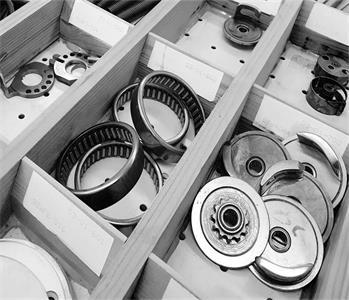
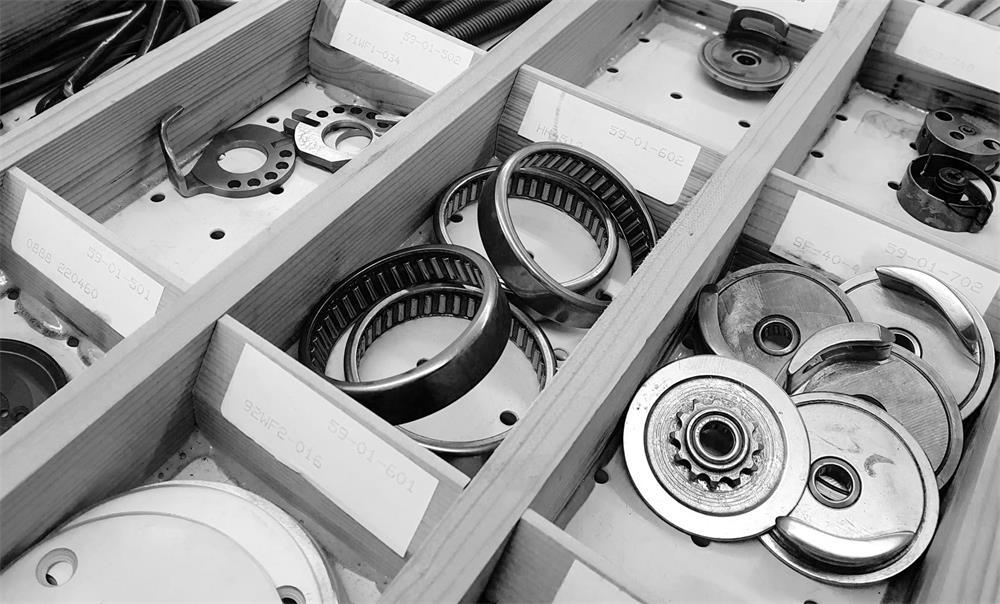
The surface treatment of machine parts is a process method that uses edge new technologies of modern physics, chemistry, metal science, and heat treatment to change the condition and properties of the surface of the parts to meet the predetermined performance requirements. In order to improve the strength of the machine parts, the following surface treatment processes are usually used to promote the processing of the parts to ensure the final quality.
Surface quenching
Surface quenching refers to a heat treatment method that uses rapid heating to austenitize the surface layer and then performs rapid cooling (quenching) to harden the surface without changing the chemical composition and core structure of the steel.
Sandblasting
The process of using the impact of high-speed sand flow to clean and roughen the surface of the substrate. Compressed air is used as power to form a high-speed jet beam to spray the spray material (copper ore, quartz sand, emery sand, iron sand, Hainan sand) at high speed to the surface of the workpiece to be treated so that the appearance or shape of the outer surface of the workpiece surface is changed.
Knurling
Knurling is the use of hard rollers or rollers to press on the surface of the rotating workpiece at room temperature and move along the direction of the generatrix to plastically deform and harden the surface of the workpiece to obtain an accurate, smooth, and strengthened surface, or the treatment of a specific pattern craft.
Drawing
Under the action of external force, the metal is forced through the mold, the cross-sectional area of the metal is compressed, and the technical processing method to obtain the required cross-sectional area shape and size is called the metal wire drawing process. The tool to change the shape and size is called a wire drawing die. Wire drawing can be made into straight grain, random grain, corrugated, thread, and so on according to the needs of decoration.
(1) Straight wire drawing
Refers to the machining of straight lines on the metal surface by machine friction.
(2) Random pattern drawing
It is an irregular, non-obvious matte silk pattern obtained by moving the metal plate back and forth and left and right under the high-speed copper wire brush. This kind of processing has higher requirements on the surface of the metal plate.
(3) Corrugated wire drawing
Generally, it is made on a brushing machine or a rubbing machine. Using the axial movement of the upper group of grinding rollers, the surface of the metal plate is rubbed to obtain wave patterns.
(4) Thread drawing
It uses a small motor with a circular felt on the shaft, fixes it on the table, at an angle of about 60 degrees with the edge of the table, and makes a carriage with a fixed metal plate, and sticks a piece on the carriage. Polyester film with straight edges is used to limit the progress of the thread. Using the rotation of the felt and the linear movement of the carriage, a thread pattern with the same width is rubbed on the surface of the metal plate.
Polishing
Polishing is a finishing method to modify the surface of parts. Generally, only a smooth surface can be obtained, and the original processing accuracy cannot be improved or even maintained. Depending on the pre-processing conditions, the Ra value after polishing can reach 1.6~0.008 mm. According to the different implementation principles, it can be divided into the following types.
(1) Machine polishing
A high-speed rotating flexible polishing wheel and extremely fine abrasives are used to roll and micro-cut the surface of the workpiece to achieve polishing. The polishing wheel is made of multiple layers of canvas, felt or leather, and is used for polishing larger parts.
(2) Barrel polishing and vibration polishing
Put the workpiece, abrasive and polishing liquid into the drum or vibrating box, the drum rolls slowly or the vibrating box vibrates, so that the workpiece and the workpiece, the workpiece and the abrasive rub against each other, plus the chemical action of the polishing liquid, to remove the oil and rust layer on the surface of the workpiece.
Grind away the convex peaks, so as to obtain a smooth surface. It is used for the polishing of small and large parts. The latter has higher productivity and a better polishing effect than the former.
(3) Bio-polishing
Bio-polishing is a finishing process that uses cellulose to improve the surface of cellulosic fiber products to achieve long-lasting anti-pilling and increase the smoothness and softness of the fabric. Bio-polishing is to remove the fine fibers protruding from the surface of the yarn. When these fine fibers are removed, they will not fuzz and pill, the color is brighter, and the reduction of surface fluff makes the cloth surface smoother.
Laser surface strengthening
Laser surface strengthening is to use a focused laser beam to shoot the surface of the steel part to heat the extremely thin material on the surface of the workpiece to a temperature above the phase transition temperature or the melting point in a very short time and then cool it in a very short time to harden the surface of the workpiece.
Laser surface strengthening can be divided into laser phase change strengthening treatment, laser surface alloying treatment, and laser cladding treatment.
Laser surface strengthening has a small heat-affected zone, small deformation, and easy operation. It is mainly used for locally strengthened parts, such as blanking dies, crankshafts, cams, camshafts, spline shafts, precision instrument guides, high-speed steel tools, gears, and internal combustion engines cylinder liner, etc.
The above surface treatments change the morphology, phase composition, microstructure, defect state, and stress state of the material surface through physical and chemical methods. If you want to know more about machine parts, please contact us for a comprehensive solution.
With excellent R&D technology and superb craftsmanship, we have quickly become one of the leading parts suppliers. We uphold the concept of putting customers first, and provide users with high-quality products in a variety of specifications and models. We have carried out strict treatment on the craftsmanship and details of the products and can provide users with high-quality products. If you are interested in our machine parts, please contact us immediately!