What Are the Procedures for Cleaning Machine Parts?
- Share
- Issue Time
- Dec 28,2021
Summary
This article will share the specific process of cleaning machine parts so that everyone can better understand the details and precautions of cleaning machine parts.
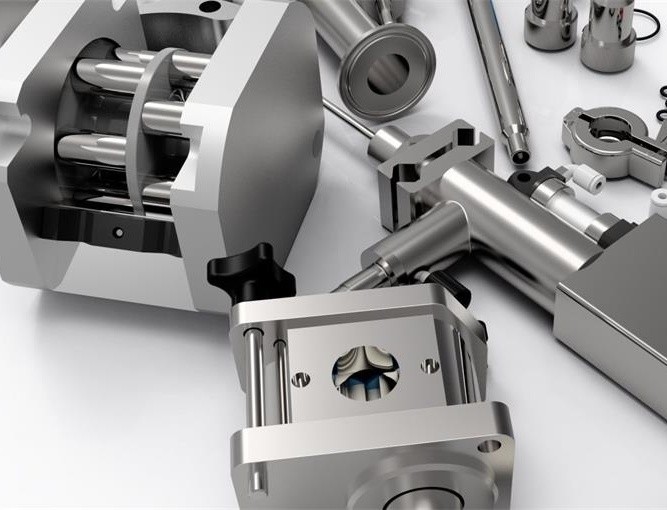

Cleaning the disassembled machine parts is an important part of repair work. Cleaning methods and cleaning quality will have an important impact on the accuracy of parts identification, equipment repair quality, repair costs, and service life. The cleaning process of machine parts includes the following steps.
1. Degreasing
To remove oil stains on parts, cleaning fluids such as organic solvents, alkaline solutions, chemical cleaning fluids, etc. are often used. Cleaning methods include scrubbing, dipping, spraying, gas-phase cleaning, and ultrasonic cleaning. There are manual cleaning and mechanical cleaning for cleaning.
The common scrubbing method in the repair of mechanical equipment is to put the parts in a container filled with kerosene, light diesel oil, or chemical cleaning agents, and scrub with cotton yarn or brush with a brush to remove oil stains on the surface of the parts.
This method is easy to operate, simple in equipment, but low inefficiency. It is used for decreasing the working surfaces of small and medium-sized parts produced in single and small batches and large parts. Generally, gasoline should not be used as a cleaning agent, because of its fat-dissolving properties, it will easily cause fires.
Spray cleaning is to spray cleaning fluid with a certain pressure and temperature onto the surface of the parts to remove oil stains. This method has a good cleaning effect and high productivity, but the equipment is complicated, and it is suitable for cleaning parts with less complicated shapes and heavy grease on the surface.
Different cleaning agents should be used to clean parts of different materials and oil stains produced by different lubricating materials. To clean animal and vegetable oils, the alkaline solution can be used, because it saponifies with an alkaline solution to produce soap and glycerin to dissolve in water.
However, alkaline solutions are corrosive to different metals in varying degrees, especially to aluminum. Therefore, different formulas should be used to clean different metal parts.
Mineral oil is insoluble in alkaline solution, so to clean the mineral oil grease on the surface of the part, an emulsifier must be added to make the grease form an emulsion and separate from the surface of the part. In order to accelerate the process of removing grease, heating, stirring, pressure spray cleaning, ultrasonic cleaning and other measures can be adopted.
2. Derusting
Corrosion substances on the surface of parts, such as surface corrosion of steel parts, must be completely removed in order to ensure the quality of the repair during the repair of mechanical equipment. According to the specific situation, currently, mechanical, chemical, and electrochemical methods are mainly used for removal.
(1) Derusting by mechanical method
Use mechanical friction, cutting, etc. to remove the rust layer on the surface of the part. Common methods include brushing, grinding, polishing, sandblasting, etc. The rusty surface can be polished manually in small batch production or repair; in batch production or where conditions permit, machines can be used to remove rust, such as electric polishing, polishing, rolling, etc.
Sandblasting rust removal is to use compressed air to spray sand of a certain size on the rusted surface of the parts through a spray gun. It not only removes rust quickly but also prepares the surface for painting, spraying, electroplating, and other processes. After sandblasting The surface can meet the requirements of a clean surface with a certain degree of roughness, thereby improving the bonding force of the covering layer and the part.
(2) Chemical rust removal
Use some acidic solutions to dissolve the oxides on the metal surface to achieve the purpose of rust removal. The chemical solutions currently used are mainly sulfuric acid, hydrochloric acid, phosphoric acid, or their mixed solutions, with a small amount of corrosion inhibitor added.
In order to ensure the derusting effect, the solution is generally heated to a certain temperature, the time is strictly controlled, and an appropriate formula must be adapted according to the material of the trusted part.
(3) Electrochemical derusting
Electrochemical rust removal is also called electrolytic corrosion. This method can save chemicals, has high dust removal efficiency and good rust removal quality, but consumes a lot of energy and complex equipment. The commonly used method is anodic corrosion, that is, the corroded part is used as the anode, so it is called anodic corrosion. There is also cathodic corrosion, that is, the rusted part is used as the cathode, and lead or lead-antimony alloy is used as the anode.
The main disadvantage of anodic corrosion is that when the current density is too high, it is easy to corrode excessively and damage the surface of the part, so it is suitable for parts with a simple appearance. Cathodic corrosion has no over-corrosion problem, but hydrogen is easy to penetrate into the metal, causing hydrogen embrittlement and reducing the plasticity of parts.
3. Remove the coating layer
Removal of the protective coating layer on the surface of the part can be completely or partially removed according to the damage degree of the coating layer and the requirements of the protective coating layer. After the coating layer is removed, it should be rinsed and ready to be sprayed to refresh the coating.
The removal method is generally to use hand tools, such as scrapers, sandpaper, steel wire brushes, or portable electric or pneumatic tools for scraping, grinding, brushing, etc. Chemical methods can be used when conditions permit, that is, various prepared organic solvents, alkaline solution paint removers, etc. When using alkaline solution paint remover, apply the brush to the paint layer of the part to dissolve and soften it, and then remove it with hand tools.
Pay special attention to safety when using organic solvents to remove paint. The work site should be ventilated and isolated from fire. The operator should wear protective equipment. After the work is over, hands should be washed to prevent poisoning. When using an alkaline solution paint remover, do not let aluminum parts, leather, rubber, and felt parts come in contact with them to avoid corrosion. Operators should wear alkali-resistant gloves to avoid injury from skin contact.
The cleaning of machine parts is related to the performance in the future, so we must strictly follow these procedures. As an expert in machine parts research for many years, ZHONGKEN can give you some guiding reference opinions to a certain extent.
We are an experienced parts manufacturer. We have leading R&D technology and excellent manufacturing technology and can control the quality of products in all aspects. Our products are used in various machinery and equipment and have excellent application performance in all walks of life. Our thoughtful after-sales service has also received unanimous praise from customers all over the world. If you want to buy our machine parts, please contact us immediately!