What You Need to Know About Surface Treatment and Coating of Metal Parts?
- Share
- Issue Time
- Mar 22,2022
Summary
Metal parts are used in a variety of applications and often require some degree of surface improvement before use. Here are some questions about surface preparation and coatings for you.
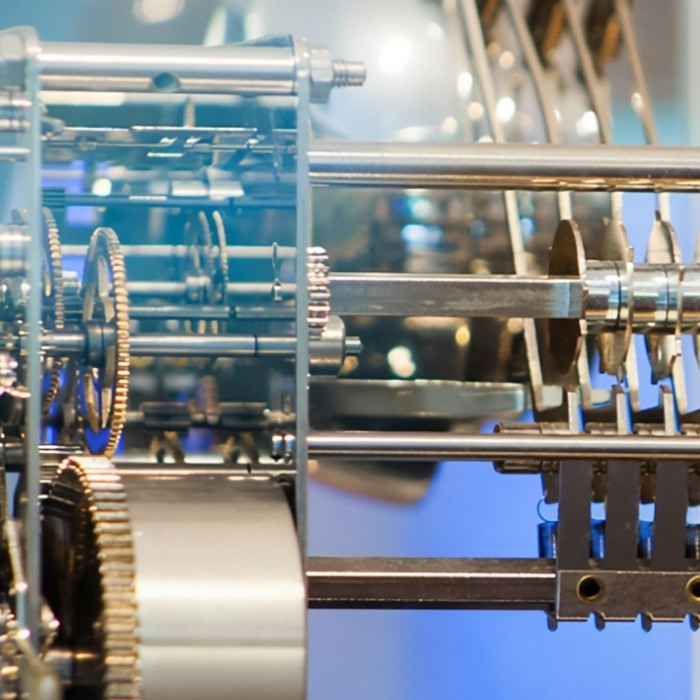
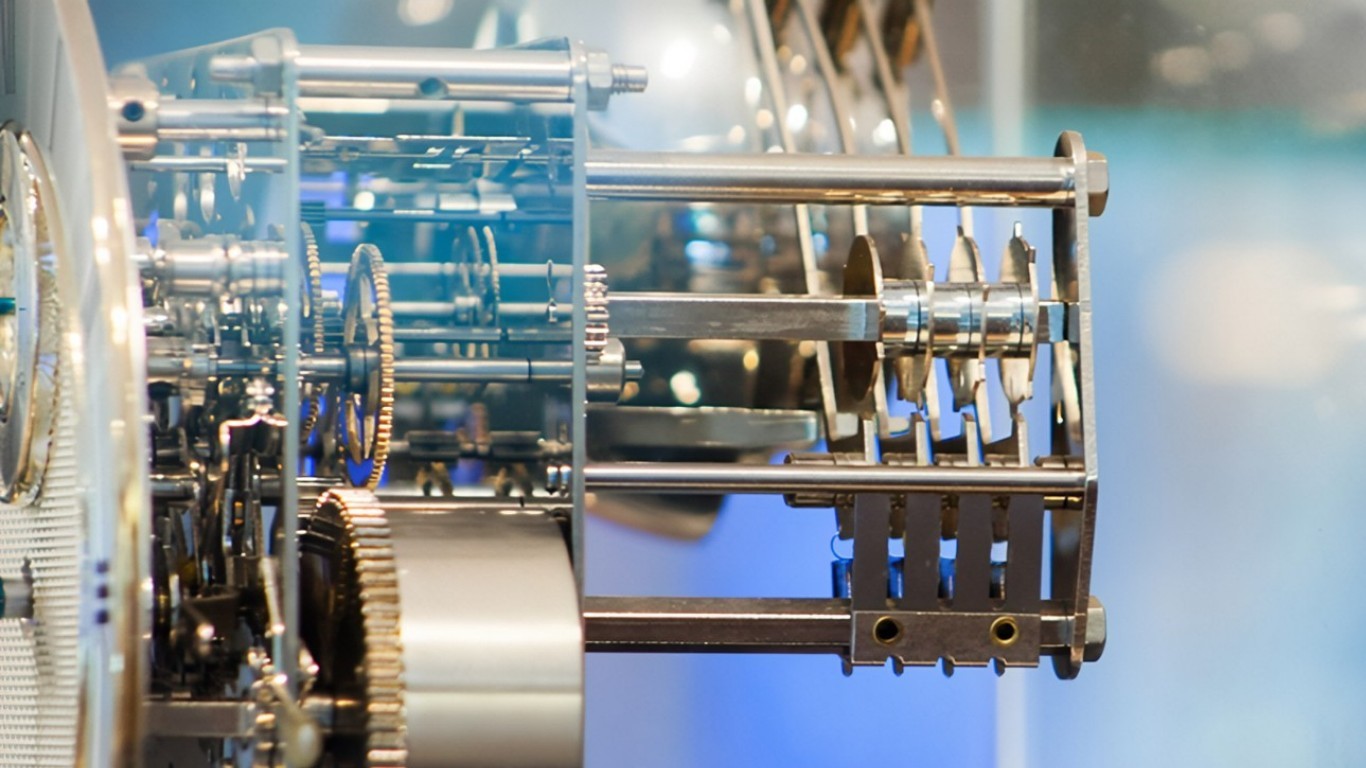
Metal parts are used in a variety of applications and often require some degree of surface improvement before use. Surface treatment or polishing is essential as it ensures that the metal part is adequately prepared for its intended application. By eliminating defects on the part's surface, corrosion is minimized, and the coating material adheres properly and enhances the part's overall appearance.
The initial surface roughness depends on the material type (stainless steel, titanium, plastic) and the method used to manufacture the part (machining, injection molding, casting). Various secondary operations such as heat treatment, welding, sandblasting, etc. can also affect the surface before finishing. Understanding these factors can help in customizing the surface treatment process and preparing metal parts for surface coating.
While the surface finish is often used to reduce overall surface roughness, there are some situations where an ultra-smooth finish is not ideal. Surface treatments can be used to create different surface textures, such as dotted or matte finishes, to improve the adhesion of certain coatings.
Surface treatment steps
As mentioned above, preparing metal parts for surface treatment can vary greatly. The type of surface coating applied and the final intended use of the product will determine the level of finish required. Regardless of the coating, metal surfaces must be free of contaminants such as grease, oil, and corrosion that parts may encounter during manufacturing or shipping.
In order to obtain a clean surface, metal parts may go through the following process.
Descaling
Heat treatment or cast scale removal is the first step in preparing a part for surface coating. It allows a complete visual inspection of the surface for any manufacturing defects or voids. For example, descaling can expose casting defects, such as those found on cast magnesium parts in the automotive industry. Parts found to be defective can be reworked or scrapped instead of continuing to be sent through the entire finishing and coating process.
Deburring
Next, deburr the inside and outside of the part using vibratory finishing or centrifugal drum finishing. The deburring process is designed to remove machining burrs and other defects built upon the machined surface and is a necessary prerequisite for surface coating. Deburring also improves product quality, increases part life, and enhances aesthetics.
Polishing
After the deburring operation is complete, both the inner and outer surfaces of the part go through the pre-polishing and final polishing stages. Polishing is essential as it continues to improve the surface using less and less rough media, resulting in a uniform, smooth and clean surface. Electropolishing or other chemical processes may be used in cases where certain complex interior areas cannot be reached by rolling media. Surface coatings adhere more completely to refined surfaces, increasing the life and corrosion resistance of metal components.
Surface coating application
After an appropriate surface roughness is achieved, a surface coating can be applied. The type of surface coating applied is generally determined by its application. Common surface coating types for metal parts include powder coating, chrome plating, titanium nitride, and DLC.
What are the commonly used metal surface treatment methods for precision machining?
Metal plating
Metalworkers use machines to coat thin layers of materials such as copper, nickel, chromium, or aluminum. Sometimes metal plating involves gold, platinum, and silver for decorative purposes. Metallic coatings improve corrosion resistance, surface friction, and appearance
Brushed metal
Metal plating does not eliminate surface defects, so in some cases, brushed metal is a better choice. Abrasive belts or wire brushes can create textures that hide surface imperfections.
Powder coating
Powder coating is decorative and more durable than paint. The dried plastic powder can be melted and applied to surfaces in a variety of colors and textures.
Hot black
The machine paints black oxide on the outside of the product and paints a uniform matte black. Auto parts, tools, and firearms are often heated blackened.
Metal grinding
Grinders wear edges and smooth surfaces.
Metal vibration finishing
Operators use vibrating drums with abrasive particles to handle small pieces that need cleaning. Vibration finishing removes sharp edges and eliminates imperfections.
Two-part epoxy resin
Two-component resins provide smooth surfaces for fiberglass, steel, wood, and aluminum. They add a moisture barrier and a reflective high-gloss finish for long-term UV protection.
Anodizing
The operator coats the aluminum surface with aluminum oxide. The aluminum oxide layer is corrosion and wear-resistant. It costs less than comparable finishes and requires little maintenance. UV light won't damage it, it won't chip or peel, and it won't show fingerprints. It is available in different colors and finishes.
Galvanized
Galvanized material is coated with a zinc protective layer. The most common process is to coat the product by dipping it in a bath of molten zinc. Galvanizing costs less than many other finishing methods and has a long life expectancy. One benefit of galvanizing is that if it gets damaged, the rest of the area is still protected, so minor damage doesn't need to be repaired.
Sandblasting
Operators use sand or other abrasives at high speeds to create smooth textures. There are different types of sandblasting depending on the level of cleanliness required by the project.
If you would like to know more about how to prepare metal parts for surface coating, please contact us.
Zhongken Machinery Co., Ltd. is a professional precision CNC parts processing manufacturer. Since its establishment, it has been committed to precision mechanical parts processing, mold parts processing, casting, sheet metal parts processing, and export. Over the years, we have been providing high-precision machining parts and high-quality services to overseas customers, and are deeply trusted and supported by overseas customers. We aim to meet customer needs and continue to provide customers with satisfactory products and high-quality services. Machinery members look forward to serving you and establishing long-term and stable cooperative relations.