Tips for Reducing the Deformation of Aluminum Parts During CNC Machining
- Share
- Issue Time
- Apr 19,2022
Summary
Aluminum is an active metal, and it is very easy to deform during processing. Below we give some suggestions from the actual operation to reduce the probability of deformation of aluminum parts.
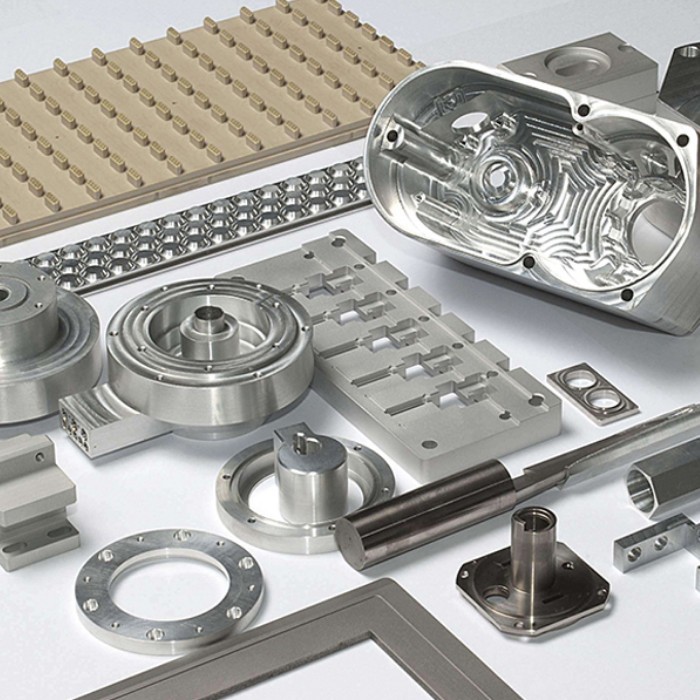
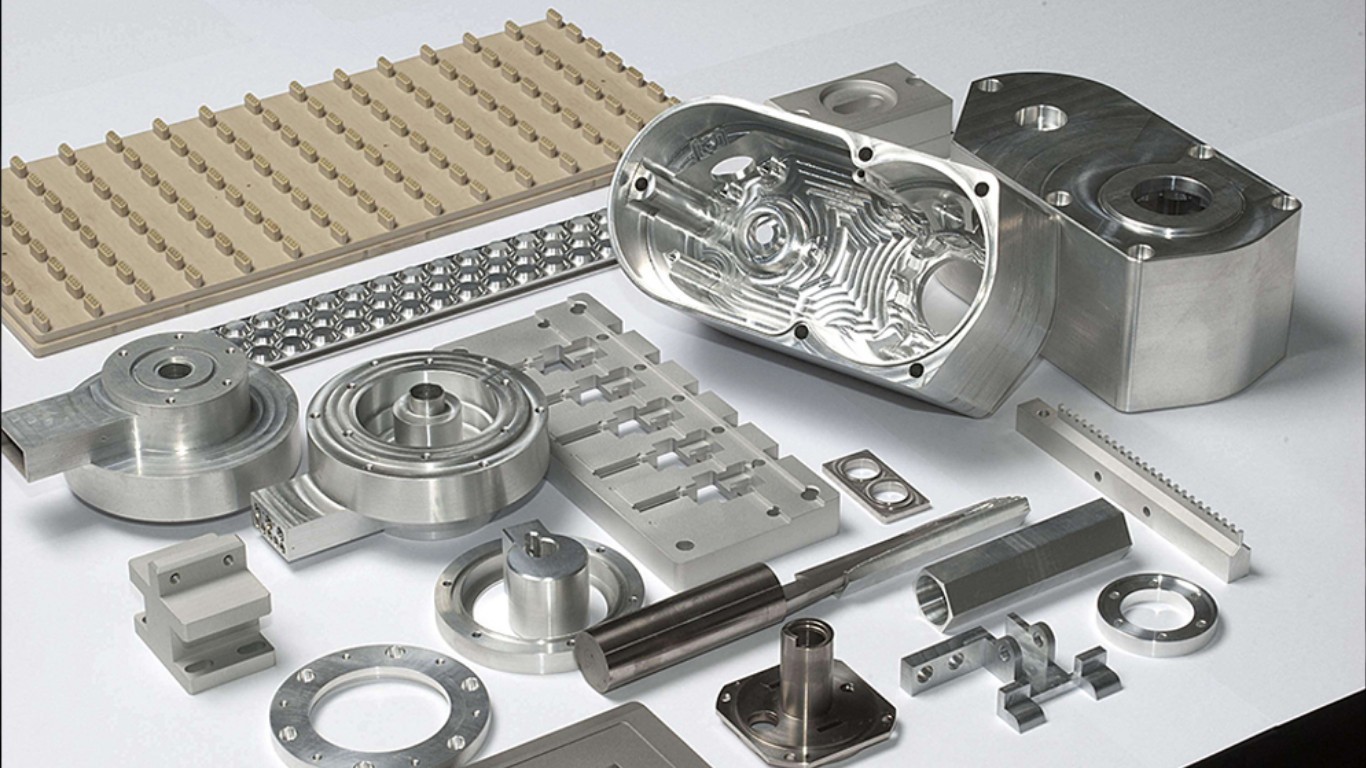
Aluminum is an active metal, and it is very easy to deform during processing. Below we give some suggestions from the actual operation to reduce the probability of deformation of CNC aluminum parts.
1. For parts with a large machining allowance, in order to make them have better heat dissipation conditions during processing and avoid heat concentration, symmetrical processing should be used during processing.
If a 90mm thick sheet needs to be processed to 60mm, After milling one side, immediately mill the other side, and add it to the final size at one time, and the flatness will reach 5mm; if the symmetrical processing of repeated feeding is used, each side is processed twice to the final size, and the flatness can be guaranteed to reach 0.3mm.
2. If there are multiple cavities on the plate parts, it is not suitable to use the sequential processing method of one cavity and one cavity during processing, which will easily cause uneven stress on the parts and cause deformation. Multi-layer processing is adopted, and each layer is processed to all the cavities at the same time, and then the next layer is processed to make the parts evenly stressed and reduce deformation.
3. The cutting force and cutting heat are reduced by changing the cutting amount. Among the three elements of the cutting amount, the amount of back-engagement has a great influence on the cutting force. If the machining allowance is too large, the cutting force of one pass is too large, which will not only deform the parts but also affect the rigidity of the machine tool spindle and reduce the durability of the tool.
If the number of knives to be eaten by the back is reduced, the production efficiency will be greatly reduced. However, high-speed milling is used in CNC machining, which can overcome this problem. While reducing the amount of back cutting, as long as the feed is increased accordingly and the speed of the machine tool is increased, the cutting force can be reduced and the processing efficiency can be guaranteed at the same time.
4. The order of cutting tools should also be paid attention to. Roughing emphasizes improving the processing efficiency and pursuing the removal rate per unit time. Generally, up-cut milling can be used, that is, the excess material on the surface of the blank is removed at the fastest speed and the shortest time. Form the geometric contour required for finishing.
While finishing emphasizes high precision and high quality, it is advisable to use down milling. Because the cutting thickness of the cutter teeth gradually decreases from the maximum to zero during down milling, the degree of work hardening is greatly reduced, and the degree of deformation of the part is also reduced.
5. Thin-walled workpieces are deformed due to clamping during processing, and even finishing is unavoidable. In order to reduce the deformation of the workpiece to a minimum, you can loosen the pressing piece before finishing the final size, so that the workpiece can freely return to its original state, and then slightly press it, as long as the workpiece can be clamped (completely). According to the hand feel), the ideal processing effect can be obtained in this way.
In short, the action point of the clamping force is preferably on the support surface, and the clamping force should act in the direction of the workpiece with good rigidity. On the premise of ensuring that the workpiece is not loose, the smaller the clamping force, the better.
6. When machining parts with a cavity, try not to let the milling cutter plunge directly into the part like a drill when machining the cavity, which will cause the milling cutter to have insufficient space for chip storage and unsmooth chip removal, resulting in overheating, expansion, and collapse of the parts. Knives, broken knives, and other unfavorable phenomena.
First, drill the hole with a drill of the same size as the milling cutter or one size larger, and then mill it with the milling cutter. Alternatively, CAM software can be used to produce helical rundown programs.
The main factor affecting the machining accuracy and surface quality of aluminum parts are that such parts are prone to deformation during the machining process, which requires the operator to have certain operating experience and skills. If you have any questions about the above issues or need to customize CNC aluminum parts, please contact us.
ZHONGKEN is a professional custom CNC machining parts supplier in China, we have been committed to precision mechanical parts processing, mold parts processing, casting, sheet metal parts processing, and export. Over the years, we have been providing high-precision machining parts and high-quality services to overseas customers, and are deeply trusted and supported by overseas customers.